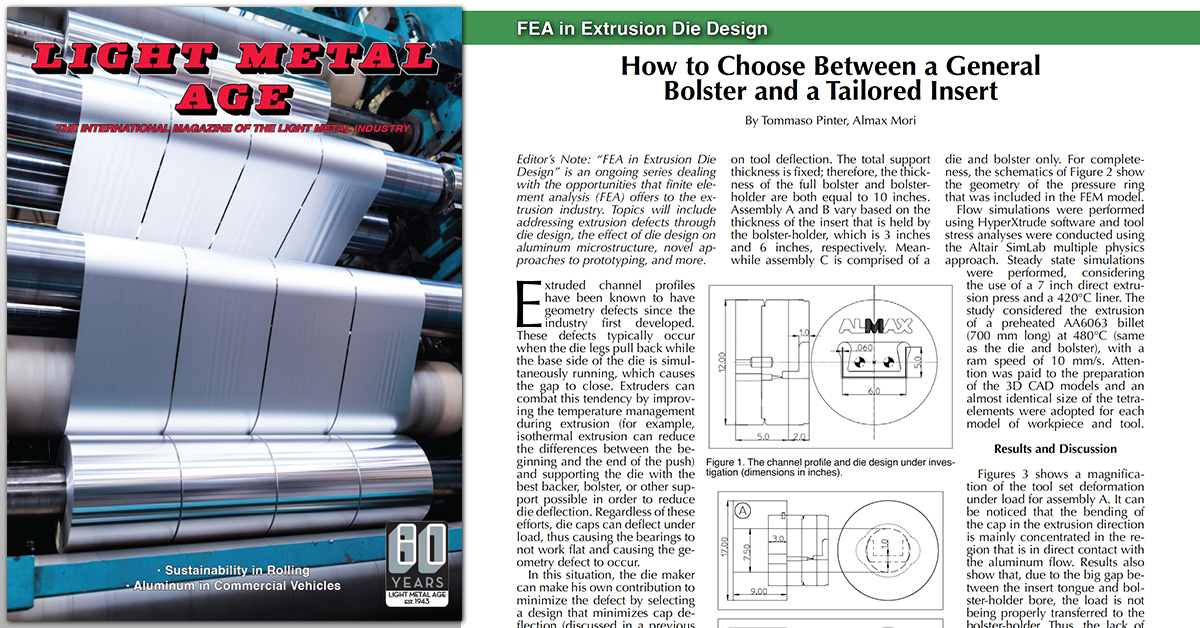
How to Choose Between a General Bolster and a Tailored Insert
Abstract
Extruded channel profiles have been known to have geometry defects since the industry first developed. These defects typically occur when the die legs pull back while the base side of the die is simultaneously running, which causes the gap to close. Extruders can combat this tendency by improving the temperature management during extrusion (for example, isothermal extrusion can reduce the differences between the beginning and the end of the push) and supporting the die with the best backer, bolster, or other support possible in order to reduce die deflection. Regardless of these efforts, die caps can deflect under load, thus causing the bearings to not work flat and causing the geometry defect to occur. In this situation, the die maker can make his own contribution to minimize the defect by selecting a design that minimizes cap deflection (discussed in a previous article from the August 2019 issue of Light Metal Age), as well as helping the extruder to choose the best support option among the ones available. This article will discuss the process of selecting the best support option. In particular, the article will investigate the difference in given support among tailored inserts and general ”U” shaped full bolsters.