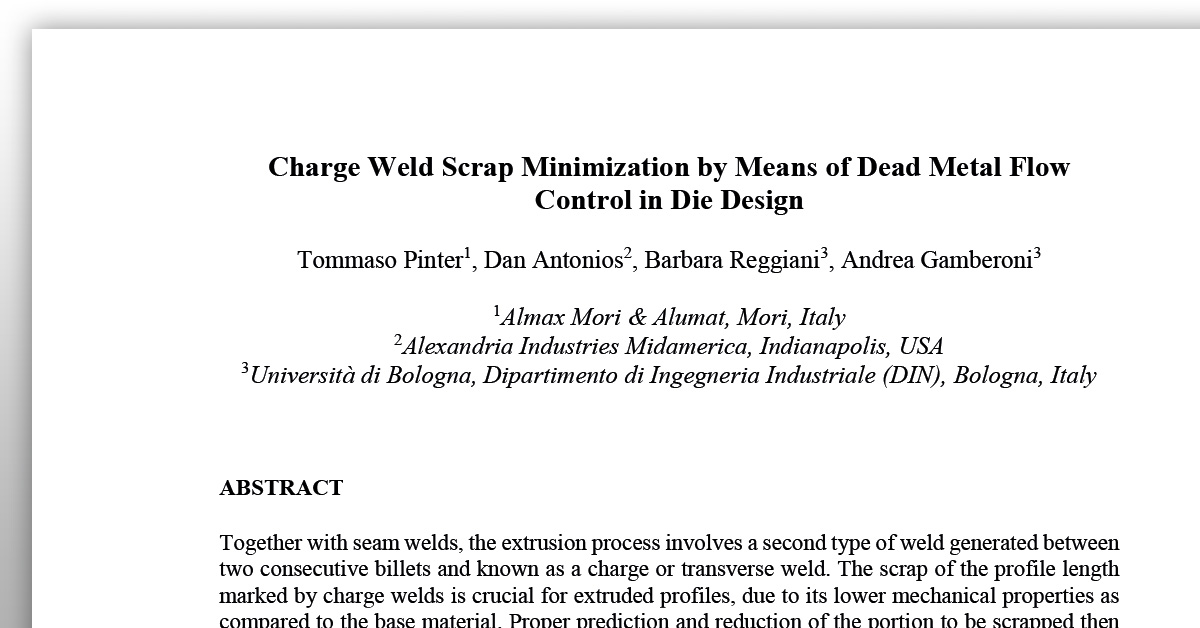
Charge Weld Scrap Minimization by Means of Dead Metal Flow Control in Die Design
Abstract
Together with seam welds, the extrusion process involves a second type of weld generated between two consecutive billets and known as a charge or transverse weld. The scrap of the profile length marked by charge welds is crucial for extruded profiles, due to its lower mechanical properties as compared to the base material. Proper prediction and reduction of the portion to be scrapped then become mandatory, not only for the final user of the profile, in order to avoid in-service product failures, but also for extruders and die makers to increase process efficiency. The extension of the charge weld, otherwise called front-end defect, is strongly influenced and driven by the die geometry. In this context, the present work examined the dynamics of the dead metal zones in hollow extrusion dies through the use of FE analyses and looked at the effect of their minimization of the front-end defect without altering the overall process efficiency. The starting point was the industrial experimental verification of the FE model used to predict the charge weld evolution for the initial die configuration. Then, the benefits of an innovative die design approach were quantitatively evaluated by means of an extensive numerical campaign both in terms of recovery and productivity, achieving a final optimized die design that allowed the extruder to reduce the charge weld scrap. The sensitivity analysis of the results to process parameters (ram speed, billet temperature and alloy) was also performed.
(Tommaso Pinter, Dan Antonios, Barbara Reggiani, Andrea Gamberoni)